Production of biodiesel in a supercritical process
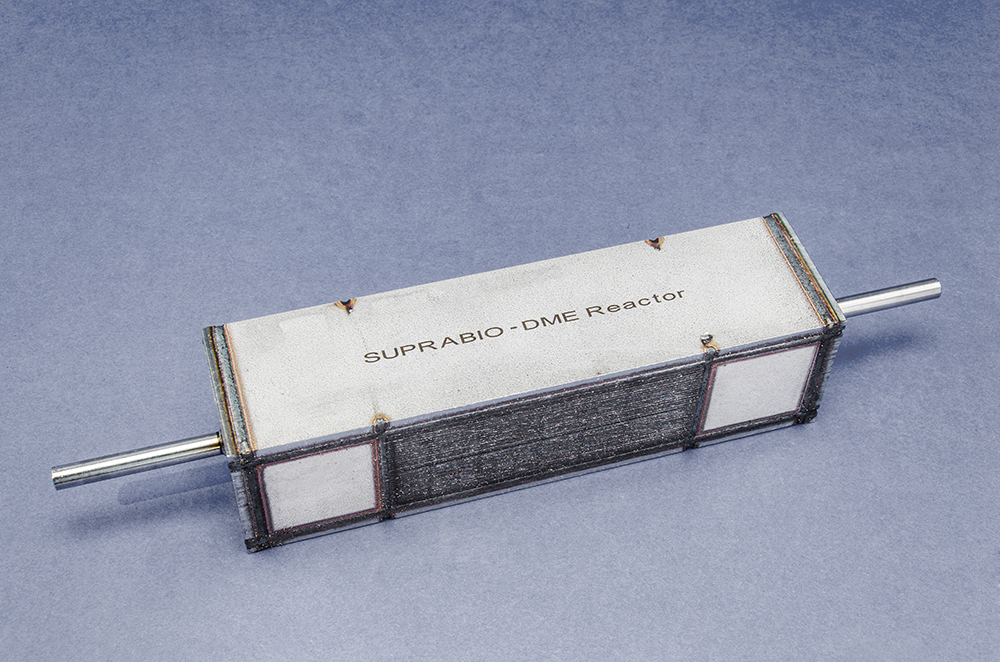
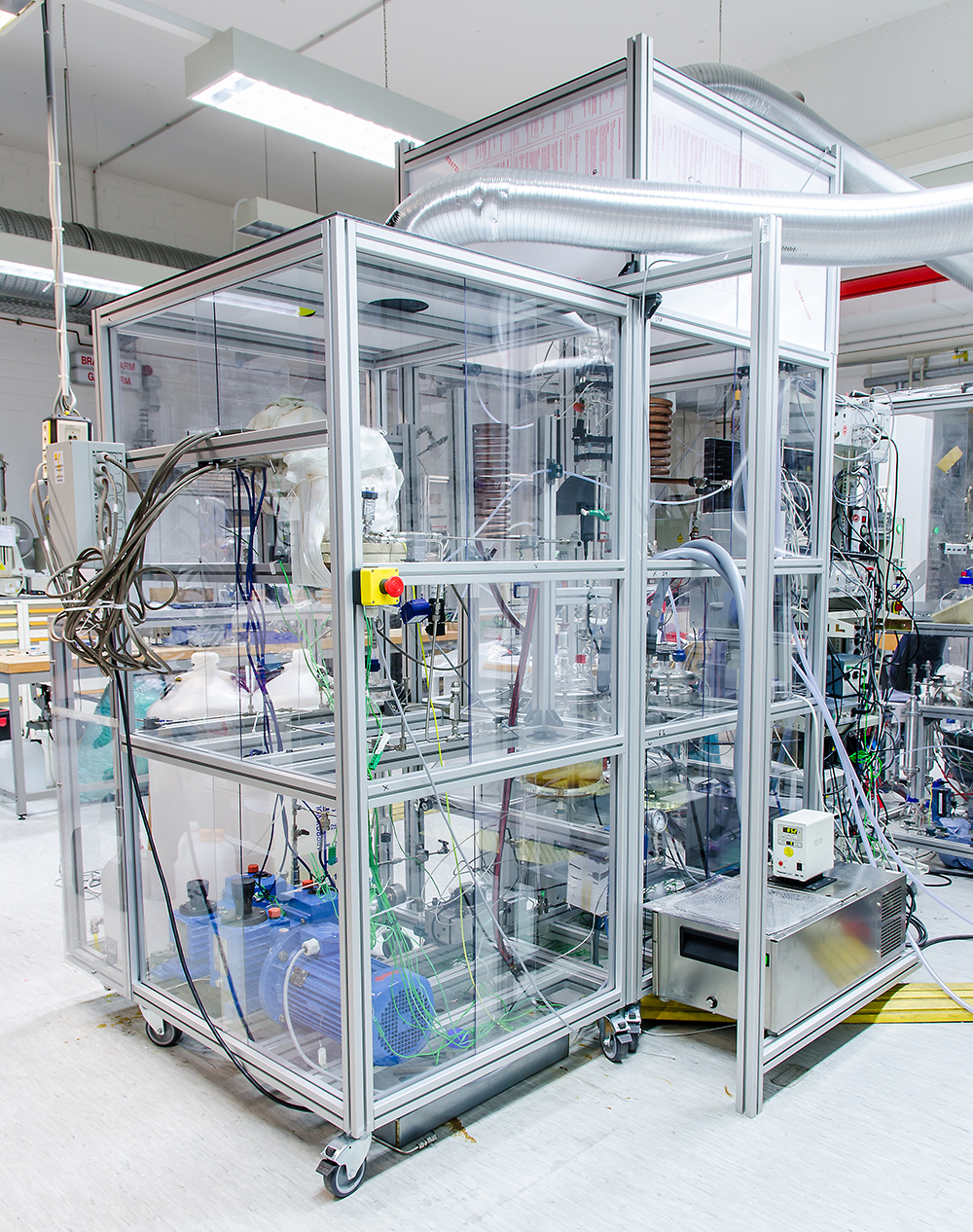
Biodiesel from vegetable oils is the best known biofuel in Germany. With around 1.8 million tons it accounts for approximately two-thirds of the German biofuel sales volume, mostly as an additive to diesel fuel. Compared to mineral oil-based diesel, biodiesel has lower emissions. It is produced from renewable raw materials, is biodegradable and has good lubricating properties, which is advantageous for the use of low-sulfur diesel fuel.
Functionalities
Within the framework of the project, a small laboratory plant shall be developed and tested, which can produce biodiesel from different vegetable oils and used cooking oils in a supercritical process at significantly higher reaction rates and other expected benefits. ‘Supercritical’ defines the thermodynamic state of substances at and beyond of a specific constellation of temperature and pressure, in which the properties of liquids and gases merge without phase separation.
Properties and application areas
Biodiesel production as a supercritical process with heterogeneous catalysts has been investigated for the first time in a continuously operated complete plant. Due to the supercritical process management the reaction time is reduced. At the same time, several process steps such as the recovery of the homogeneous catalyst become redundant. The transesterification of vegetable oil, which is quite common in biodiesel production, is carried out with supercritical methanol. Instead of the homogeneous catalysts used otherwise, we rely on innovative heterogeneous catalysts that are applied as a coating in microscale reactors. Thanks to the new concept, transesterification rates are being increased, while the reactor size as well as water consumption are reduced. The sensitivity of the process against traces of water in the raw material decreases. Besides this, the lower demand of methanol, the higher purity of the by-product glycerin and the long-term stability of the catalyst are expected advantages. When replacing methanol by ethanol, the already improved environmental compatibility can be increased even further. Although the process takes place at high pressures and temperatures, process optimization ensures a total energy consumption which is significantly lower compared to conventional methods. We were responsible for the development of the plant, the process and the novel catalyst technology. We also carried out tests with various vegetable oils and, for instance, used cooking oils as well.
Our research & development services
Together with our customers, we are engaged in developing decentralized plants which produce biodiesel from waste materials on-site without long transportation routes, depending on the application.
We are also developing concepts for the production of basic chemicals such as methanol and higher alcohols as well as for the production of fuels from renewable energy sources.
BIOGO project website
Funded by: Federal Ministry of Food and Agriculture, following a decision of the German Bundestag and supported by the Energy and Climate Fund of the Federal Government through the Agency for Renewable Resources. (FNR, FKZ: 22 400111).